Are you a welder who wants to stay safe and protected from hazards? Whether you are a novice or experienced welder, using protective aprons is essential for your safety.
You’ll learn in this guide how to select the right apron, best practices for use and more – so you can keep welding safely.
The use of protective aprons for welders is of utmost importance in order to ensure the safety and well-being of welders when working with dangerous tools and extreme temperatures. Welding without enhanced protection can result in serious injury or worse. In this guide, readers will be provided with an overview of the types of protective aprons available, an explanation as to why welding aprons are important, and tips on how to choose the right apron for your application.
Welding has been used since ancient times as a joining technique but over time it has evolved and become a metalwork process relied upon in numerous industries. As technology continues to advance, so too do the tools at welders’ disposal. However, due to the immense heat produced during welding operations those working with such materials must always dress accordingly – this includes wearing protective aprons or jackets when appropriate. Protective clothing ensures nearby skin won’t come into contact with hot sparks or extreme temperatures which could cause serious burns or fires. Moreover, despite having technological advancements like auto-darkening helmets that provide eye protection from ultraviolet radiation still don’t completely eliminate the risk of danger posed by welding processes – again making it imperative that welders wear recommended protective clothing such as an apron while working on projects.
Definition of protective aprons for welders
Welders wear protective aprons to protect themselves from sparks, heat, and other hazards associated with welding. These aprons are made from materials that will not catch fire or melt when exposed to extreme temperatures. They can also provide protection from electric shocks by providing insulation for the body. A protective apron is typically one of the first pieces of safety gear a welder wears when beginning their workday.
The U.S. Occupational Safety and Health Administration (OSHA) mandates that welders use personal protective equipment (PPE) when welding in order to protect themselves against potential accidents or injuries while on the job. Welding aprons are an important component of these required PPE items – they are designed to provide physical protection to the welder’s body while covering areas that may be prone to exposure such as the chest and groin area.
Welders should always inspect their protective aprons prior to working in order to ensure that they do not contain any damages or flaws that could potentially lead to an accident on the job site. Damaged aprons should be replaced immediately in order to guarantee the highest quality of protection for welders performing their daily tasks. Furthermore, OSHA recommends regular cleaning and inspection of all PPE used by welders on a frequent basis in order for them to remain safe and operate effectively throughout their day-to-day work activities.
Purpose of protective aprons
Protective aprons are an important piece of safety equipment that is essential for welders across different industries. They provide multiple layers of protection against harmful radiation, sparks, and electricity generated due to welding processes.
Protective aprons are also the primary layer of protection for the interviewer’s upper body for further hazards and heat that arise during welding work. Not only does it protect the skin and clothes from being damaged due to accidental sparks and droplets of molten metal, but it also prevents welding lines from becoming tangled up in clothing or jewelry.
Protective aprons should be carefully selected keeping in mind various conditions such as temperature, visibility, water resistance, static resistance etc. Quality protective aprons should also be produced with strong fibers that can act as a guard against flame splatter while providing comfortable ventilation at the same time.
The right protective apron will not only protect welders’ upper body but also reduce any distractions during welding operations which increases efficiency and reliability on the job site.
Importance of using protective aprons
Welders are exposed to several hazards on a daily basis. To ensure their safety, welders must wear protective gear while they work. Protective aprons are a key piece of this gear, providing an extra layer of protection against arcs, sparks, and metal fragments that may be produced during the welding process. In addition to being flame-resistant and heat-resistant, protective aprons should provide impact protection too.
The use of protective aprons has been proven to reduce the risk of occupational injuries, particularly when paired with other types of PPE such as helmets and face shields. Not only do they provide facemask coverage from flying debris, but they also protect against chemical splashes, large flying particulate matter (like large pieces of slag), and heat generated from welding processes like arc welding or grinding. Protective aprons can also help deflect radiation produced during low voltage welding operations; which is vital for controlling radiative exposure in workers who perform these types of tasks over long periods of time.
In short, wearing a protective apron is an important part of overall safety measures for welders. By providing extra layers of protection from both physical and radiative hazards, welding aprons help create a safe working environment for welders handling hazardous materials on a regular basis – ensuring welders can focus entirely on the task at hand without worrying about their own safety or health in the long run.
Factors to Consider When Choosing a Protective Apron for Welding
When it comes to choosing the right protective apron for welding, there are several factors that need to be taken into consideration. These factors include:
- Material: The most common materials used for welders’ protective aprons are leather, nylon, and cotton. Leather is the most durable material and will provide the highest amount of protection from sparks and other hazards related to welding. Nylon is lighter weight and cheaper than leather, but does not provide as much protection. Cotton aprons are lightweight, breathable, and affordable, but do not offer as much protection as leather or nylon aprons.
- Design: Welders’ aprons come in a variety of styles including full-length ones which cover the lower body from waist to mid-calf; bib style which offers more chest coverage than a standard waist-level apron; adjustable neck straps; reinforced pockets; and adjustable chest straps. Ensure that your chosen apron fits well according to your body measurements so that it can offer optimal protection while still allowing you flexibility when working with welding tools.
- Protection: Look for an apron that offers maximum protection by covering all exposed skin when welding or grinding/slicing metal with power tools and equipment. A good quality apron should be fire resistant to protect against any sparks upon contact with the material being worked on during welding operations. Additionally, fully encased leg zippers help ensure complete leg coverage from spark incidents while standing or kneeling during operations on hot surfaces or material piles/slag piles while grinding/slicing/welding metal products into shapes or parts of objects concerned with manufacturing products used in construction projects requiring high degrees of safety precautions due to hazardous working environments arising frequently in these industries such as offshore oilrig parts manufactureres operating under challenging conditions like deep sea industrial operations at precarious locations around marine environments etcetera.
Type of welding
Welders use protective aprons to protect themselves from the hazards of welding. Different types of welding require different levels of protection due to the various materials involved and the resulting heat, sparks, and slag created during the process. The type of apron needed will depend on the type of welding being done and whether it’s going to be used indoors or outdoors.
- Type of Welding: Different types of welding procedures require different levels of protection by way of protective aprons:
-Arc Welding – Uses electric current which produces an intense heat that can cause sparks and molten metal splatter which can easily penetrate an inadequate apron.
-Gas or Oxy-Acetylene Welding – Creates an intense local heat which produces extreme sparks, molten droplets and chunks, capable of damaging unprotected skin.
-Stick Welding – Produces more fumes than other types when outdoors but less arc produced so lower risk is posed compared to Arc and Gas Welding indoors.
-TIG (Tungsten Inert Gas) welding – Involves feeding a tungsten electrode into the weld puddle while producing no sparks, producing less emission compared to other methods and less risk is posed when working indoors.
Working environment
The working environment of a welder plays an important role in how they select protection equipment. Protective aprons can provide additional protection when working in hotter and more hazardous environments, while they are often not necessary for lighter duty welding tasks. Some general guidelines to consider when selecting protective aprons include:
- Hot work requires more protection – Welders often face hot molten metal and sparks, so generating sufficient body heat can easily occur. Therefore, some form of physical resistance between the body and the hot surface is essential for welding operations which involve higher temperatures. Protective aprons can help manage this issue by providing additional insulation or heat-resistant material between the welder and the surrounding heat source.
- Use when applicable to heavier duty welding tasks – Protective aprons are most effective for welding operations that involve generating higher temperatures or dealing with harder materials such as steel or aluminum alloys. For lighter applications where no additional insulation is needed, a simple safety vest will be sufficient to protect against minor cuts, burns and sparks from flying objects.
- Weight should be adjusted according to task – Heavier protective aprons are often preferred as they better protect against intense heat sources such as foundry furnaces, making them ideal for many major processing applications in industries like manufacturing, mining and construction. However, too much weight creates discomfort during long periods of wear, so only use heavier materials when necessary to avoid causing unnecessary strain on the worker’s muscles and joints.
Comfort
The comfort of the welder’s apron is also worth considering. The apron should fit securely but not be so tight as to hamper movement. It should feel durable against the skin – not too hard and certainly not too loose. It should also feature fabric that is light and breathable to keep the wearer cool while welding. Sewn-in, adjustable straps are also preferred to belts which can be uncomfortable after extended periods of use and can slip around during welding situations.
Additionally, look for aprons with a lining designed to create an added layer of thermal protection, ensuring ultimate comfort while blocking sparks and debris from harming the wearer underneath it.
Durability
Durability is a key factor to consider when selecting a protective welding apron. Welders often work in hostile environments, with temperatures approaching thousands of degrees Fahrenheit and exposure to dangerous sparks, embers and chemicals. Many welding aprons have been designed with water-resistant, fire-resistant and chemical-resistant materials that are specifically designed to provide maximum protection during the toughest welding tasks.
It is important to choose an apron that offers flexibility yet won’t shrink or tear easily so that it can be used for extended periods of time under any conditions. Look for aprons made from durable materials such as Kevlar®, vinyl coated cotton, heavy duty leather and neoprene. Also be sure to evaluate adjustable features such as bibs, length and straps for convenience and comfort in various welding jobs.
Proper Use and Care of Protective Aprons for Welders
After purchasing a protective apron for welding, it is important to take the necessary steps to ensure that it is used and maintained properly. The following provides instructions on how to get maximum protection from your protective apron.
– Prior to use, inspect your protective apron for any rips, tears, holes or loose stitching. Replace or repair damaged aprons immediately; otherwise, they cannot provide adequate protection against heat and sparks.
– When donning the protective apron, ensure that it fits comfortably and securely; if it feels too tight or restricts movement in any way then adjustments should be made before beginning work.
– Protective aprons made with leather must be treated with an oil based solution after each use in order to keep them water resistant and strong. Always follow the manufacturer’s recommendations when applying oil treatments.
– Additionally, all metal components (i.e., buckles) should be examined regularly for corrosion and replaced as needed in order to continue receiving proper protection from your protective apron.
– Protective aprons should be hung upside down between uses in order to help prevent moisture accumulation which can lead to bacterial growth or damage of fabrics due to shrinking or stretching over time. When storing your apron for extended periods of time without use, it should still be allowed to hang freely in order to maintain its dimensions and level of protection during future uses.
– Lastly, replace your protective apron if there is any visible wear or tear; worn down aprons cannot provide the same level of protection as new ones and risk exposing welders potentially hazardous materials while working.
Putting on the apron
Putting on protective aprons for welding is an important safety measure. Welding aprons are usually made of leather or fire-retardant fabric and should fit snugly, without restricting the welder’s movement. They help to protect the upper body from heat, sparks, and shrapnel, and may also contain pockets for tools or supplies. It is essential to check that the apron is in good condition before each use, as any damage could reduce its effectiveness in protecting the wearer.
When putting on the apron it should be worn outside other protective clothing and equipment so that it does not interfere with mobility or create any gaps which may be exposed to risk. The straps of the apron need to be securely fastened so it remains firmly in place while welding. It is also recommended to wear full-length pants beneath the welding apron as they can offer extra protection from sparks and splatter that may occur during the operation.
Adjusting the fit
A good fit is the most important aspect of protecting yourself from molten spatter and other welding hazards. The waistband should sit about 1-2 inches above your hipbones for best performance, and you should ensure that the straps are firmly fastened and don’t slip down. Some newer aprons use adjustable straps to ensure a snug fit; this also allows you to quickly adjust the size if necessary when different types of clothing are being worn underneath.
When purchasing your apron, consider how easy it is to open and close each time so you can make sure your body is adequately protected. Of course, comfort also plays a key role; look for an apron that has interior padding or shoulder straps that disperse pressure evenly over your shoulders or back. This will help reduce fatigue over long periods of welding.
Inspecting for damage
When inspecting for damage and any signs of wear and tear, it is important to take a look at the entire length of the protective apron. Several areas require close attention to ensure maximum protection. These include securely-sewn straps, hooks, buckles and seams, as well as any protective overlays or finishes that have been added to the apron.
Strap/Buckle: Inspecting the strap/buckle ensures that it will remain secure when being worn. Check all fasteners for any fraying or wear which could cause them to come apart during use.
Seams: Seams need to be robust and intact in order to provide adequate protection during welding activities. Look out for any signs of separation due to heavy usage or tearing which could cause the apron to come apart in sections.
Overlays/Finishes: Depending on the type of protective apron being used, you may find overlays or finishes added for increased protection from sparks and splatter. Make sure that these additional features are still intact so that they can continue providing adequate protection from heat and splatter.
Conclusion
In conclusion, wearing a protective apron is essential for any welder who wants to protect themselves from the dangers of welding. An apron should be made from flame retardant material, and should properly fit the area of the body being covered. It also should provide adequate coverage over areas that may be most commonly exposed. A good quality protective apron will help to reduce or eliminate both physical and chemical hazards faced by welders.
Utilizing additional protective gear, such as gloves and work boots, will add an extra layer of defense against many potential welding hazards. With proper selection and use of safe welding practices and apparel, it is possible for welders to avoid potential safety risks associated with working in this dangerous profession.
FAQ’s
What is the importance of welding apron?
Welding aprons are important in protecting the wearer from sparks, heat, and molten metal during welding.
What is the purpose of protective clothing in welding?
The purpose of protective clothing in welding is to protect the welder from hazards such as heat, sparks, and UV radiation.
Why protective shield is required in welding?
A protective shield is required in welding to protect the eyes and face of the welder from harmful UV radiation and flying debris.
What is the purpose of protective shield?
The purpose of a protective shield is to provide protection to the welder’s face and eyes from welding hazards.
What is the function of protective shield?
The function of a protective shield is to shield the welder’s eyes and face from harmful UV radiation, sparks, and flying debris.
What protection is required for welding?
Protection required for welding includes welding helmets, protective clothing, gloves, and respirators.
What are the benefits of welding shield?
The benefits of welding shield include protecting the welder’s eyes and face from harmful radiation and flying debris, which reduces the risk of injury and enhances their safety.
Why is safety important in welding?
Safety is important in welding because it involves various hazards that can cause serious injuries to the welder, and proper safety measures can help prevent accidents and injuries.
What is the importance of 5 essentials of welding?
The five essentials of welding, including cleanliness, joint fit-up, proper heat control, proper welding technique, and proper electrode selection, are important in ensuring high-quality and safe welding operations.
Why do you need protective equipment?
Protective equipment is needed to protect the welder from welding hazards, such as heat, radiation, and flying debris, and to ensure their safety during welding operations.
See more-
- Best leather aprons 2023
- Best radiation aprons 2023
- Best aprons for pottery 2023
- Best aprons for women 2023
- Best aprons 2023
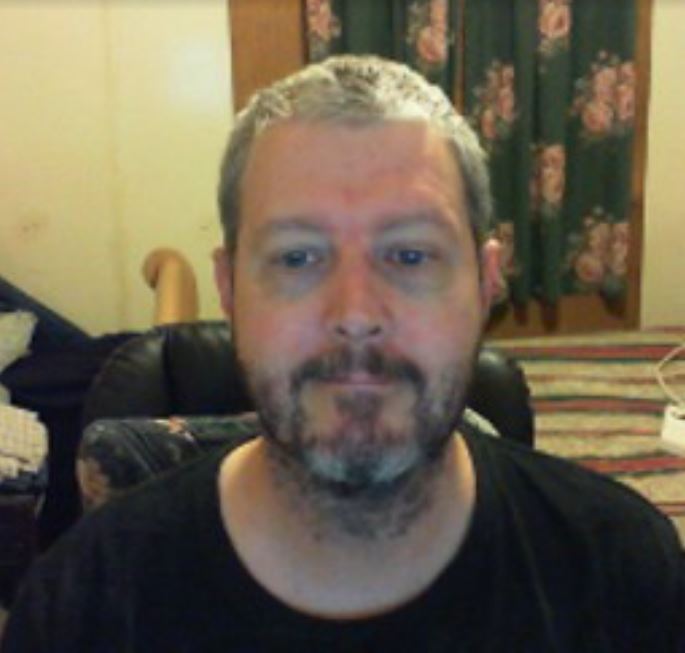
Douglas Keefer is the CEO and author of apronspalace.com and Informative Website. With his extensive knowledge and expertise in the world of aprons, he has helped thousands of people find the perfect apron for their needs. Douglas’s commitment to transparency and honesty has made apronspalace.com stand out in a sea of biased reviews and sponsored content. He is a true pioneer in the world of aprons and a passionate advocate for the culinary arts